Providing Solutions Centered on Material Supply Equipment and Robot Control Technologies for Casting Plants
Sanmei Kikou leverages its extensive experience and expertise to develop equipment that streamlines manufacturing processes in sectors such as the automotive industry and industrial machinery. We offer solutions centered around material supply systems and robotic control technologies, aiming to optimize the critical processes that take place before and after material melting.
Specifically, we design and manufacture equipment capable of handling the entire sequence—from material weighing and transportation to feeding into the melting furnace. We also actively develop new technologies to automate labor-intensive tasks that have traditionally been difficult to mechanize, delivering products that meet diverse industry demands.
Furthermore, we have begun developing equipment that supports risk assessment to enhance safety in manufacturing environments, a topic that has been gaining increasing attention in recent years. Through these efforts, we aim not only to improve workplace safety but also to ensure peace of mind for workers. Sanmei Kikou’s advanced technological capabilities and reliability have earned the trust of many clients through these initiatives.
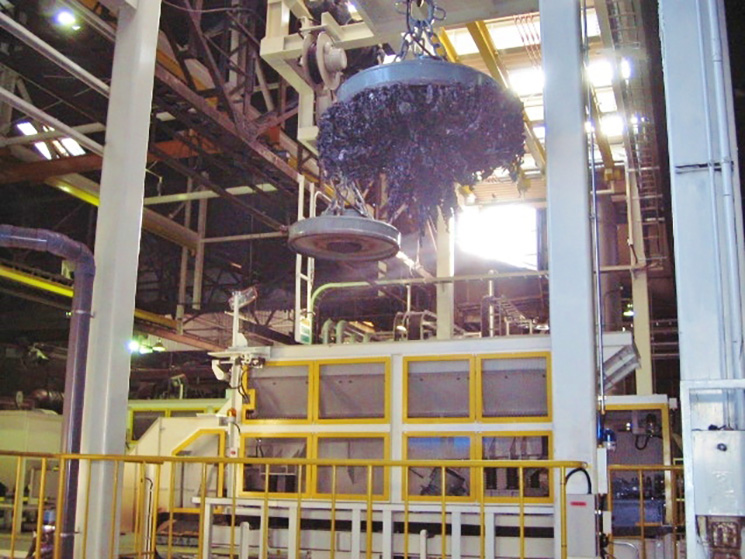
Custom-made support
At Sanmei Kikou, we go beyond standardized products to offer fully customized designs and manufacturing based on client requests. We provide optimal solutions tailored to each industry and application.
Commitment to quality
We apply strict quality control to each product, delivering reliable and durable systems. Our commitment to high quality standards ensures products that can be used with confidence over the long term.
Quick and flexible response
From development to delivery, we strive for quick and flexible responses in every process. We adapt promptly to customer requests and market changes to achieve the best possible outcomes.
Environmental Considerations
We design and manufacture with a focus on minimizing environmental impact, contributing to a sustainable society. We promote energy-efficient systems and waste-reducing production methods.
QCD and Carbon Neutrality
At Sanmei, we pursue excellence in QCD—Quality, Cost, and Delivery—while actively promoting carbon neutrality. We aim to reduce environmental impact and contribute to a sustainable future by optimizing production efficiency and introducing energy-saving technologies.
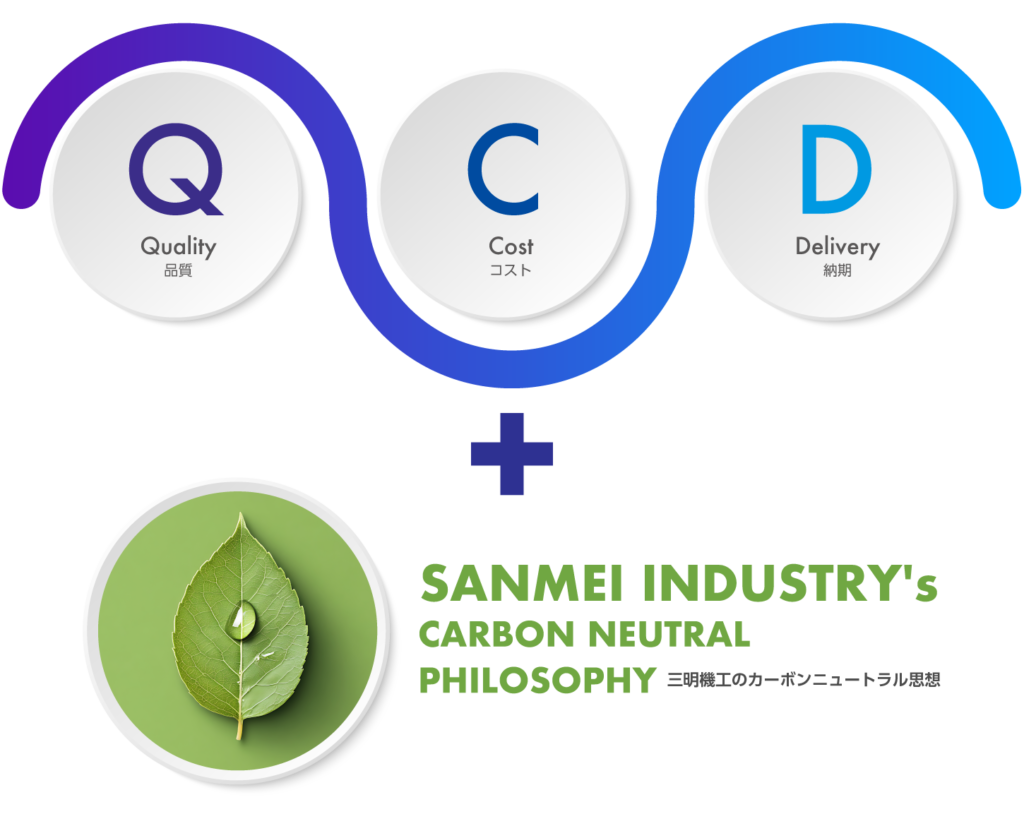